STORY電解液真空注液ポンプができるまで
身の回りにある多くの製品に使われている電池。中でもリチウムイオン電池やニッケル水素電池など、二次電池と呼ばれる充電式の電池は現在、ハイブリッドカーや携帯電話、PCなど今の時代の主要産業には欠かせない存在です。
電池には一般的に電解液という液体が入っていて、工程のどこかで電解液を入れなくてはなりません。それも一滴も漏らさず、わずかな容量をピッタリ合わせて。
長野オートメーションでは、シビアに液体をコントロールする技術を、プリンターのインク注入や液晶注液という、電池とは異なる分野で早い段階から手掛けてきました。それをベースにして二次電池の製造機器へ、さらに次の舞台へ。あらゆる分野の製造機器を手掛けるからこその視野の広さで独自技術を確立していく長野オートメーションの魅力を、電解液注液ポンプや液晶注液ポンプの開発を振り返りながら開発担当者の座談会形式でお届けします。
MEMBER参加者紹介
第一技術部 課長
平井 健一
第一技術部 係長
米沢 昌範
第一技術部
長谷川 大知
営業部
坂下 栄一
まず注液ポンプについて教えて下さい。
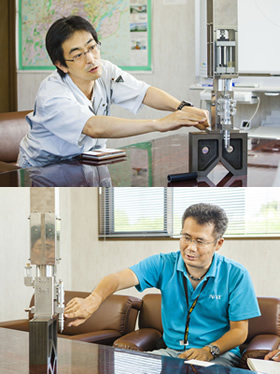
米澤 まずみずてっぽうのような筒があって、入り口から液体を引っ張り込み、出口から別の部分へ液体を出すということが、一般にプランジャーポンプとか、ディスペンサーと呼ばれるシステムです。
平井 これはすでに多くのメーカーが作っているものですが、電解液注液ポンプのベースとなった液晶注液ポンプを手がける際に最も苦労したのがメーカーの選定でした。彼(米澤)が全国のディスペンサーメーカーを片っ端から当たったのですが、発注元の希望に添えるメーカーがその時点で二社だけしかなかったのです。
米澤 液晶用ですから金属異物に極力触れさせないためにオール樹脂でつくりたい。さらに、量を制御するために真空中で液を打ちたいという希望でしたが、どのメーカーも樹脂性というところでまず無理と判断されました。これまでプランジャーポンプを樹脂で作るメーカーはどこにもなかったんです。さらに量を制御できない、制度が出ないなどの問題が出てしまって。
平井 そこで最終的にその二社のメーカーと協力して開発を進めていきました。液晶の値段は金と同じくらい高価なのですが、それまでは容器内に満たした液晶の中に、短冊状のガラスを浸すやり方を採用していて、とても無駄が多かったのです。一度使った液は再生できない。今回のディスペンサーは真空下でほとんど液垂れをしないので、無駄なく少なく打てるのが特徴です。少なく打つために先端の角度などを細かく工夫しました。
他にも開発中の困難はあったのでしょうか。
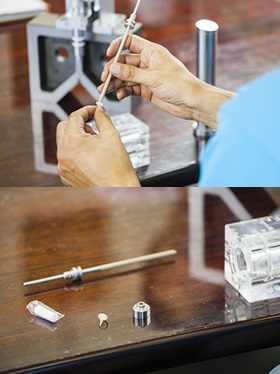
平井 実は完成して引き渡す一週間前、生産が始まる直前になって液晶内に小さなゴミがはいることがわかったんです。樹脂だから目に見えないバリが出るんですよ。
米澤 福岡まで飛んで、顕微鏡を見ながらバリを取る技術を持つメーカーにも問い合わせたり…。一週間では解決できるはずもなく、結局三ヶ月ほど時間がかかりました。
平井 五〜六通りの解決策を試したのですが、ゴミの混入は防げなくて、最後に、もともとテフロンのパッキンが入っていたところに、ダメ元で一般的なオーリングを組み込んでみたんです。オーリングには粗いバリがあるのですが、粗すぎて内部に入らなかったのか、結局それでゴミがでなくなって。どうして最初からオーリングを使わなかったのか、その時は嬉しいのとこれで良かったのかガックリきたのと両方でしたね。
米澤 丸い形をしているオーリングを使うと、パッキン部分に空気が残って液晶内に入ってしまう不安があったので、最初は使わなかったのです。その不安をなくすために、パッキンを独自に加工してオーリングを密着させ、空気をなくす形状、空気を入れない形状にする工夫をしました。
平井 普通のメーカーが見たら、なんでこんな複雑なことをしているんだろうと思うような、細かい作業ですね。ただこの時にこれだけ苦労したので、異物が出ない樹脂のディスペンサーという点ではその後、自信を持って出せるようになりました。
従来はオートメーション機器をつくる会社ですが、この時は液体ポンプ分野にかなり特化していますね。
オートメーション機器のメーカーが、本来そこまでするものなのでしょうか。
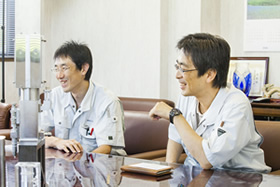
平井 当初はウチも専門メーカーに頼むつもりだったんです。ですが、ゴミの問題が出た段階で、ディスペンサーメーカーにギブアップされてしまったので、やるしかなかった。独自に開発することになったのです。直接受注した責任がありますから、うちはそこでダメだとあきらめてしまうわけにはいかないんです。 液晶注液ポンプの開発には延べ半年かかりました。最後にはゴミの問題も解決して、お客様からも「すごくきれいだね」と喜ばれました。ちょうどクリスマスイブの日、男二人、寿司屋で乾杯しましたよ(笑)。それが2004年、今から八年前のことです。
それが金属異物に触れられない電解液の注液ポンプのベースにもなったと
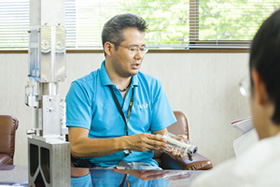
坂下 定置型の大型電池製造元からの発注があり、液晶で培った真空内での注液技術が活かせないかという話になりました。
平井 電解液注液ポンプ分野では、もともと海外に世界的なメーカーがあり、そこが独占に近いシェアを持っていました。ウチでも装置をつくるときはよく使うメーカーです。ところが五年ほど前から大型ラミネートタイプという従来の形状と異なる電池が、自動車や住宅の蓄電用途に広く使われるようになってきて、そのメーカーのポンプでは対応できなくなっていたのです。従来の電池ですと、電池の内部を真空にして電解液が浸み込みやすいやすい状態をつくり、そこに電解液を入れていきます。けれども大型ラミネートタイプは電池全体を真空環境に置いて電解液を入れなくてはならず、既存の市販ポンプは適していなかったんです。それで、真空環境下で直接電解液を注液するポンプを独自に開発することになりました。その海外メーカーのものは横型のポンプだったのですが、たまたま自分でレイアウトしたら縦のほうがいいかなと。そこで現場の皆で話をして、作ってみたのが実験の一号機ディスペンサーです。一部は液晶用のノウハウで作り、ポンプ部分や液を吸い込むバルブは今回新しく開発したものです。バルブをつける際も、吸引スピードを上げるためにさまざまなバルブを試しました。その際協力してもらったバルブメーカーとは今でも付き合いがあります。
そうした新しい技術を開発する力はどうして生まれるのでしょうか
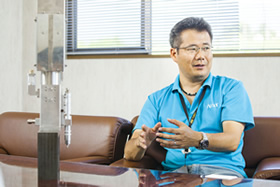
平井 他人任せにしないからでしょうか。専門メーカーに頼むだけでなく、自分たちで何年も苦しんで開発を手掛けてきたから、それがノウハウとして積み重なっているのだと思いますよ。
坂下 受けた注文は、自分たちの責任において必ず実現するから、最後までやり遂げられるというのがウチの強みです。
平井 様々なことを手掛けているから、それをベースにして新しいことに挑戦できるのだと思います。今の注液技術も幅広くやってきたことの集大成なんですよ。ディスペンサーだけ手掛けていてもこの機器は完成しなかったと思っています。
ではこれから予定している開発テーマを教えてください
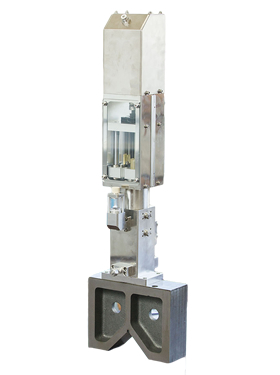
米澤 電池をつくるには様々な工程がありますが、中でも電解液を注液する工程と単位電池を積み重ねて高電圧を得るための積層の工程は、特にお客様が困っていることが多いところです。注液はこれまで長くやってきたので、これからは積層のレパートリーを増やしていきたい。将来、電池が進歩して、たとえば電解液を使わない電池になっても積層という工程は必要ですから。
平井 私が今手掛けている積層機は、現行の三分の一の大きさで倍の能力を出せないか、という要望があったものでだいぶ形になっています。 積層機には一枚ずつ重ねていく「枚葉」と「つづら折り」「袋」の三パターンがあります。できるだけ早くすべてのパターンを揃えたいと思い、頑張っています。
そのように、御社がいつも時代の中心となる分野に
即してやっていけるのはなぜなんだという声もよく聞きます
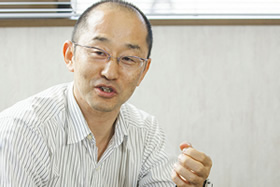
坂下 技術部や製造部がなんでもやってくれるからでしょう(笑)。営業が取ってこれるのはその時代で最も忙しく、最も伸びている会社からの仕事です。製造機器というのは、普段の作業では必要がない。新しいものを作る時、新しい分野を手掛ける時に必要なものですから。そこで断ってしまえばおしまいですが、うちは営業が取った仕事は会社が必ず作ってくれるという信頼感がありますからね。
なるほど、納得です。営業側と製作側の信頼関係があって、御社の実現力につながっているのですね。ありがとうございました。